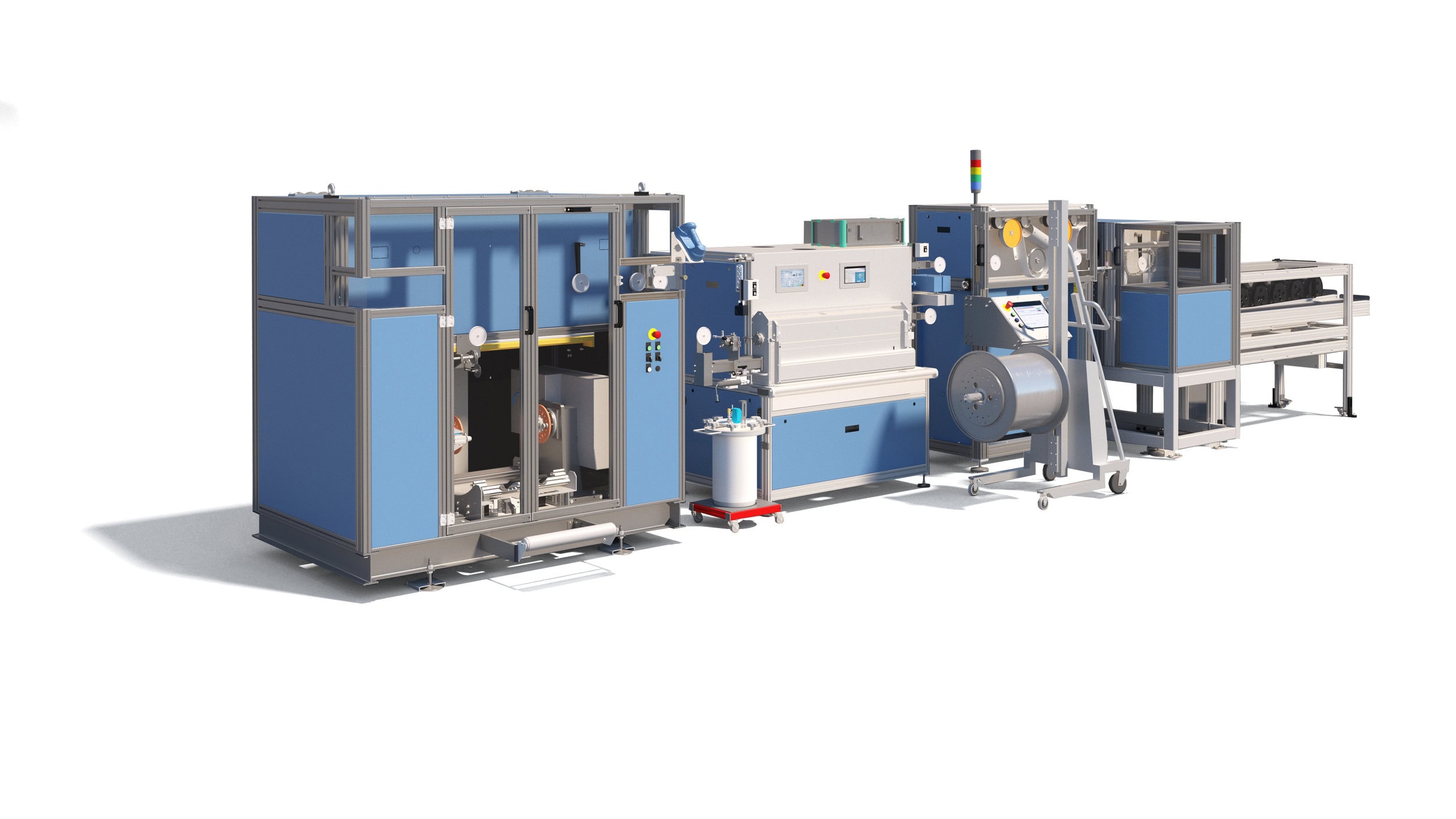
automating optical fiber proof testing and coloring
automatic reel handling system for fiber proof testing and coloring
Be faster, cheaper, less labor-intensive, sustainable, and better for the whole work environment. There are many development goals for the fiber process. All of these have become reality with the new Automatic Reel Handling System (RHS).
In a regular shift at a fiber proof testing line, there are 3 reasons for a spool change:
- regular take-up spool change
- take-up and threading in case of a fiber break
- payoff spool change
automatic reel handling system by Nextrom (RHS)
reduce 24 take-up spool changes to ZERO
An operator of a fiber proof testing line changes the take-up reel every 20 minutes. This adds up to around 24 reel changes per shift. A skilled operator needs 3 to 5 minutes to change the spool and thread the fiber. Therefore the operator spends 2 hours of the shift only on changing the spools on one machine. When using more than 4 machines, they would twiddle their thumbs instead of their spools.
The automatic reel handling system (RHS) can reduce these 24 spool changes to 0. It is included in both the OFC 30 Automated Proof Testing Line and the OFC 55 Automated Proof Testing & Coloring Line.
At the same time, the Nextrom reel handling system reduces the risk of errors and major downtime. Not to mention the scrap that can occur when poorly attaching the fiber to a reel. In the worst case, the whole spool can be damaged if the fiber is not properly attached.
automatic proof test break recovery system
In case of a break during the proof test, the operator must clean the machine, thread the fiber and change the take-up reel. On average this happens around 4 times per shift or 2 – 6 times per 1,000 km of drawn fiber.
Â
Reduce reel changes in case of fiber breaks to 0 as well, with Nextrom’s upcoming automatic proof test break recovery system. It automatically re-threads the fiber from capstan to take-up.
number 3
faster reel changes in the payoff
This leaves us with the one remaining spool change in the payoff. This occurs approximately once per shift. The automatic reel handling system (RHS) reduces even this workload by 50 %, though. The operator only needs to rethread from the payoff to the first capstan. The automatic proof test break recovery takes care of the rest.
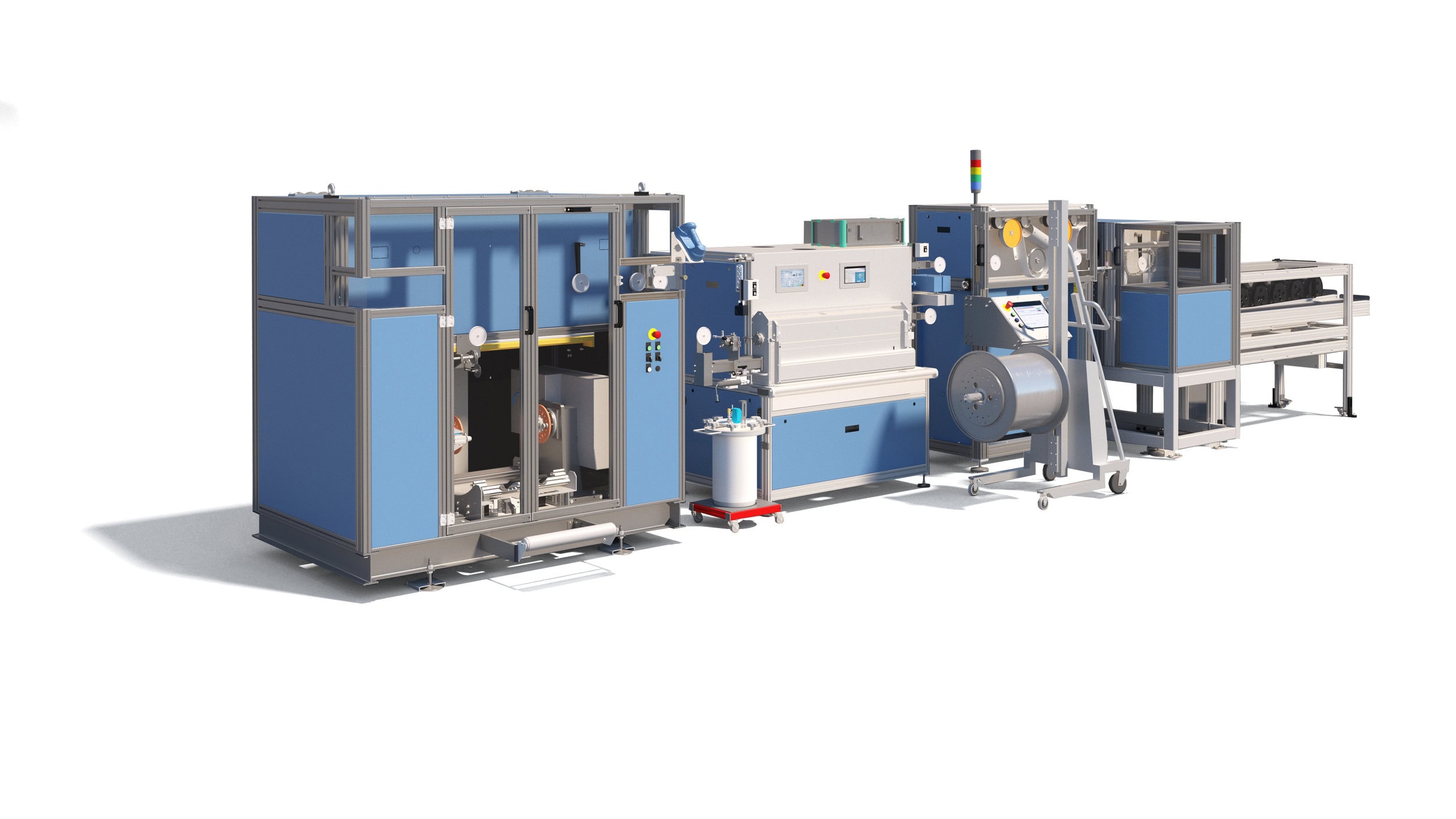
fiber coloring
in large
batches
The reworked optical fiber coloring process adds further savings potential. Color 1,000 km of proof-tested fiber with one single acrylate tank. Stop changing ink bottles thanks to the OFC 55. No need to maintain the coloring die applicator every 3 to 6 spools. The combined automated proof testing & coloring line brings exceptional efficiency to the whole process.
Silent as a whisper
Nextrom delivery spool
For a seamless automatic changeover process, Nextrom has developed its specific delivery spool. Adding even more advantages to the process:
- Reduced noise by over 10 dB at same speed.
- With only 75 dB there is no need for ear protection leading to less stress (general background noise not considered).
- Over 50 % less power consumption at a constant 3,000 m/min production speed compared to the regular spool due to the optimized design.
Advantages of the reel handling system together with the Nextrom reel
more sustainable LED curing
With LED curing in the coloring processes, power consumption will be reduced even more. These outstanding savings show our commitment to environmental sustainability and operational excellence. But there is more to come.
contact
get in
touch
with us