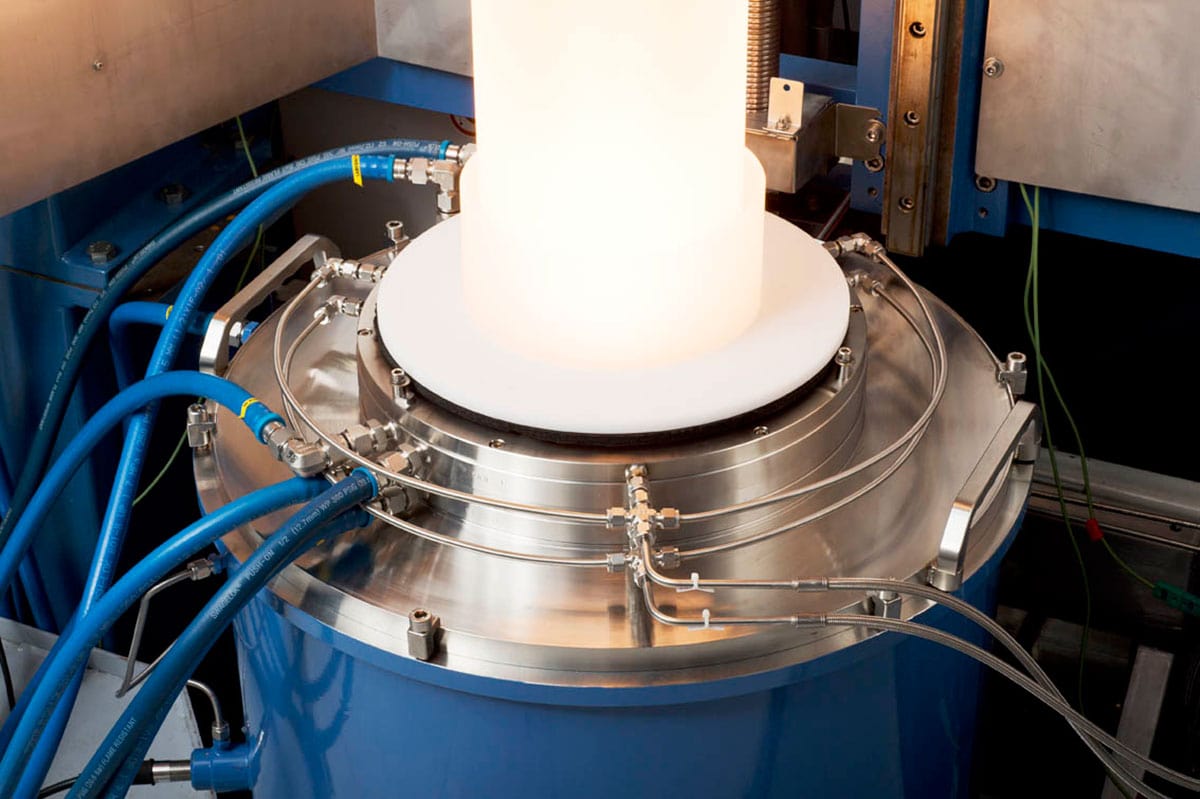
How a fiber draw furnace can cut your energy costs in half
September 26th, 2023
Learn more on how the Nextrom induction furnace can help to improve quality and reduce costs.
contact person
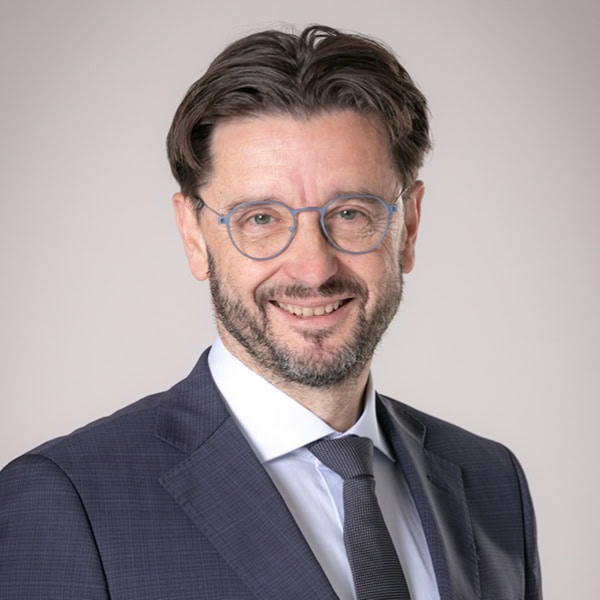
Alain Giraud
alain.giraud@rosendahlnextrom.com
share
influences on furnace energy consumption​
Optical fiber production is a resource-intensive industry. The drawing process in particular uses significant amounts of electrical power and raw materials like graphite, argon, or helium to produce high-quality fiber.
In large draw facilities, the costs of energy and raw materials affect the overall economic performance. The furnace is the central driving element of the fiber drawing process. It melts the preform at temperatures beyond 2.000 °C for the drawing process.
For a preform with a 150 mm outer diameter (OD) and a drawing speed of 2700 m/min, with common furnaces, you will need around 80 kWh or 0.5 kWh per fiber kilometer (FKM). With the currently high energy prices, this can lead to up to $ 60.000 / year / draw line only for energy.
This example shows, that the power needed for this process depends on several factors:
- fiber draw speed, typically around 3.000 m/min
- preform size, between 150 and 200 mm outer diameter (OD)
- furnace efficiency, heating method and gas usage.
the influence of the furnace
If you want to reduce costs for energy, gas, and maintenance, you need to rethink the furnace.
The furnace is the key aspect of fiber drawing, not only when it comes to energy consumption. This is especially critical when energy prices are high, as seen in recent times.
Therefore, Nextrom engineers put a lot of effort into its further development, resulting in improving the energy efficiency by 50% and reducing consumption of Argon and suppressing the need of Helium.
less energy
cut your energy consumption in half
less carbon
shrink your CO2 footprint
less noble gases
get rid of helium and reduce argon
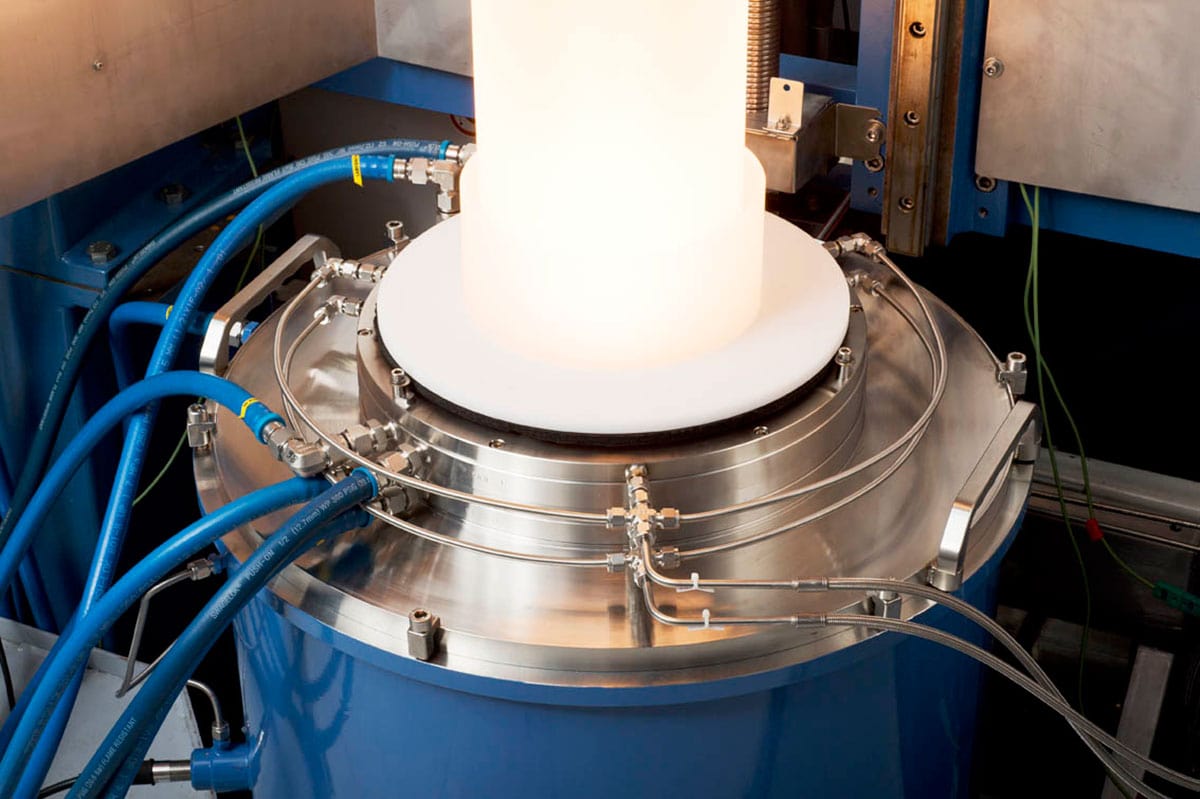
comparison
of power consumption
Nextrom Induction Furnace consumes less energy vs. Other commercially available furnaces.
use 50%
less energy
The innovative design of the furnace lets you save around 30.000 $/year/draw line.
High energy costs of 0.12 $/kWh can result in 0.06 $ per fiber kilometer. In total, this can lead up to approximately $ 60.000 per year and drawline. With an efficient Nextrom Induction Furnace, energy consumption can be reduced by up to 50%, resulting in savings of up to 0.25 kWh/FKM with an output of 1 million FKM/year/draw line.
The cost savings can therefore be significant and contribute to the overall profitability of the facility.
additional saving potential
double the lifetime of material
The new furnace offers even more potential for saving costs. In induction furnaces, we use graphite for example as a heating element. Its high thermal conductivity ensures rapid and uniform heating, while its electrical conductivity allows for the generation of electromagnetic fields necessary for induction heating. We were able to double the lifetime of the heating graphite material used in the fiber drawing process. Today we can reach a period of 4 to 6 months.
Increase fiber strength
At the same time, we could reduce the online draw breaks and offline proof testing breaks, thus increasing yields and draw productivity. Less downtime and less graphite also contribute to overall cost savings for the facility.
reduce argon consumption and make helium obsolete
Argon gas is used as a protective atmosphere in the fiber drawing furnace.
reduce noble gases
Argon gas is used as a protective atmosphere in the fiber drawing furnace. It prevents oxidation and contamination.
The built-in Nextrom Dynamic Iris isolates the furnace effectively, leading to better temperature control and insulation. This way the Argon consumption can be reduced as less oxygen is present in the furnace. The optimized structure of the furnace makes helium obsolete. A lower volume of these limited resources gives you a better chance to plan ahead in uncertain times.
reduce your carbon footprint
saving the equivalent of around 1.000 cars every year
Furnace energy consumption contributes significantly to the carbon footprint of the Optical Fiber Manufacturing Process. ​The drawing process alone indirectly generates up to 450 g CO2 per FKM. For an average fiber drawing with 20 million FKM per year, this translates to approximately 9,000 Tons of CO2 emissions per Year. This is approximately the equivalent of 1,956 passenger vehicles. The amount of CO2 emitted during the process also varies depending on the facility’s location and the energy source used. For instance, in France, where nuclear energy is the primary source of electricity, the emissions are as low as 100 g CO2/kW.
If you reduce your energy consumption, you will also reduce your carbon footprint dramatically. The saving translates to approximately 225 g CO2 per fiber kilometer, a significant reduction in emissions. By installing Efficient Nextrom Induction Furnace Technology, Energy consumption can be reduced by up to 50 %. Coming back to our 20 million fiber kilometer example, the savings would be equivalent to around 1.000 passenger vehicles
rethink the furnace for more quality and less energy
economic benefits
The last secret of the success is the high accuracy of fiber drawing technology. Today we can reach a fiber diameter tolerance within +/- 0.1 micron. This is smaller than what can be seen with a light microscope.
Upgrading to an efficient Nextrom Induction Furnace will
- tighten the tolerance to increase quality,
- reduce energy costs,
- save on maintenance,
- save on gas consumption,
- improve the overall economic performance of the facility.
For large drawing facilities producing millions of kilometers of fiber per year, the potential cost savings can be tremendous. Until this day we have equipped more than 170 draw lines worldwide with the 100% in-house designed, developed, and evaluated Nextrom Induction Furnaces for fiber drawing.
An efficient furnace will improve overall economics and reduce costs.
Contact us and we will evaluate the possibilities for an upgrade to a Nextrom Induction Furnace. It is a smart investment for any draw facility looking to improve their economic performance and contribute to a more sustainable future.
contact
get in
touch
with us