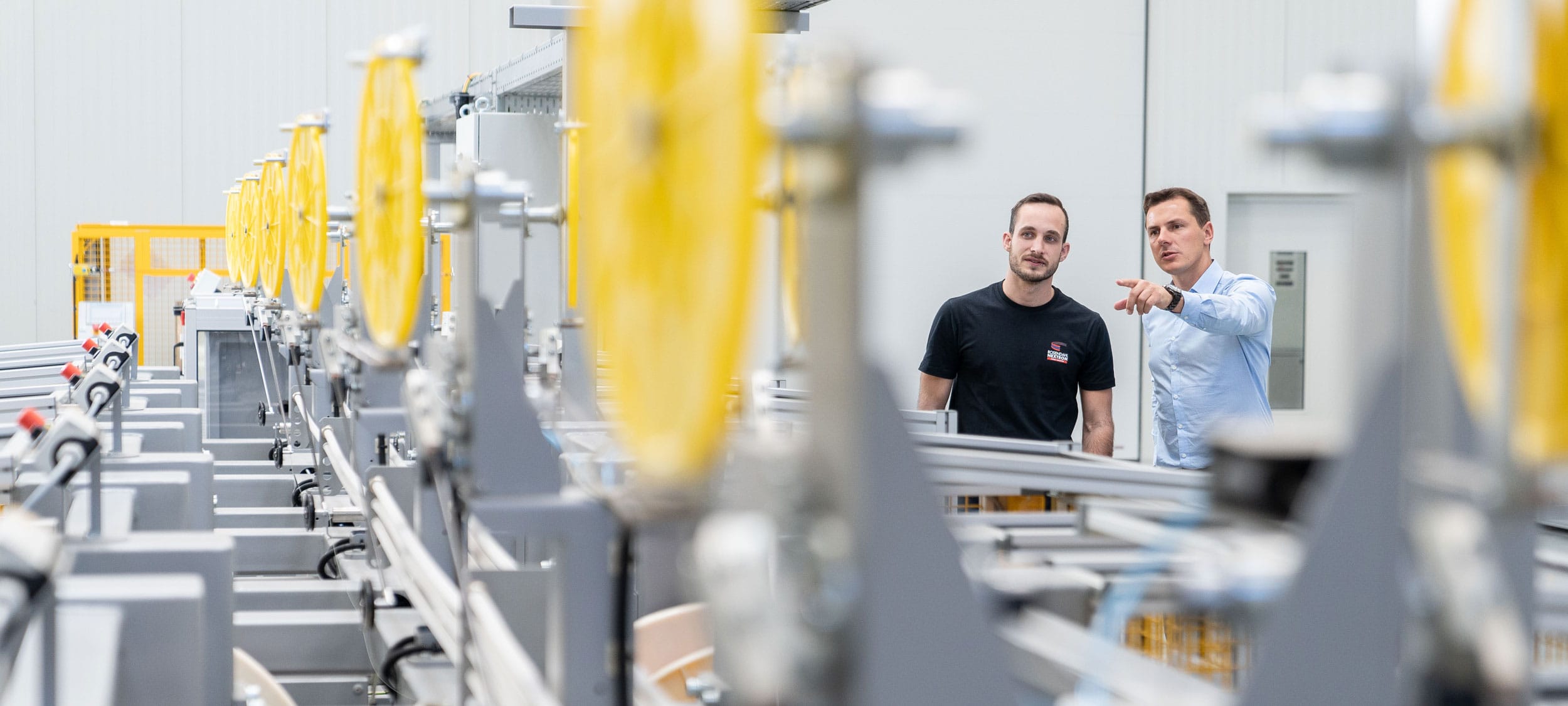
50 km nonstop stranding
July 25th, 2024
By using longer batch sizes, you can increase performance by up to 20% and, at the same time, reduce the already low scrap rate even further.
share
a performance boost by up to 20%
A stranding line processes up to 18 loose tubes. Consequently, the setup is complex, and the start-up scrap is many times higher compared to a loose tube line for the preceding production step. Given these conditions, anyone who has set up a stranding machine with 18 loose tubes aims to maximize the output from a single production run. However, to seamlessly and efficiently produce up to 50 km in one run, various factors must align.
By using longer batch sizes, you can increase performance by up to 20% and, at the same time, reduce the already low scrap rate even further.
Here is how our RL-V/OFC70 stranding line makes long batches possible:
Large spools as performance boosters
The RL-V system features tube pay-offs for reels of up to 1,000 mm, binders for large yarn bobbins with up to 290 mm in diameter and tape pay-off for pads and jumbo spools. With these matched components, extended batches are feasible without the need for operator intervention.
Gentle processing with minimal yarn tension
For consistent quality across 50 km, maintaining constant tension is crucial. This is where the low-tension binder ROBI comes into play. Equipped with integrated tension measurement, it handles the product very carefully. ROBI utilizes double cross-binding. In combination with the ultra-high speed strander DTSZ, the fastest currently available, it attains the market’s shortest reversal length, which significantly benefits cable properties.
Seamless repairs
In the rare event of a thread break or in an emergency during production, the integrated thread-cutting device is immediately activated. Thanks to its swift response, the delicate tubes remain intact. Constriction and damage are avoided. But what happens with the thread break? This issue can be resolved through synchronized line backward jogging so that the operator can secure the yarn and repair the stranded core. This procedure prevents both scrap and production downtime. The production run can almost seamlessly resume.
enhancing efficiency through extended production runs
All these practical features not only make the stranding process highly efficient but also contribute to a maintenance-friendly and scrap-reducing production in line with sustainability goals.
you may also like
contact
get in
touch
with us