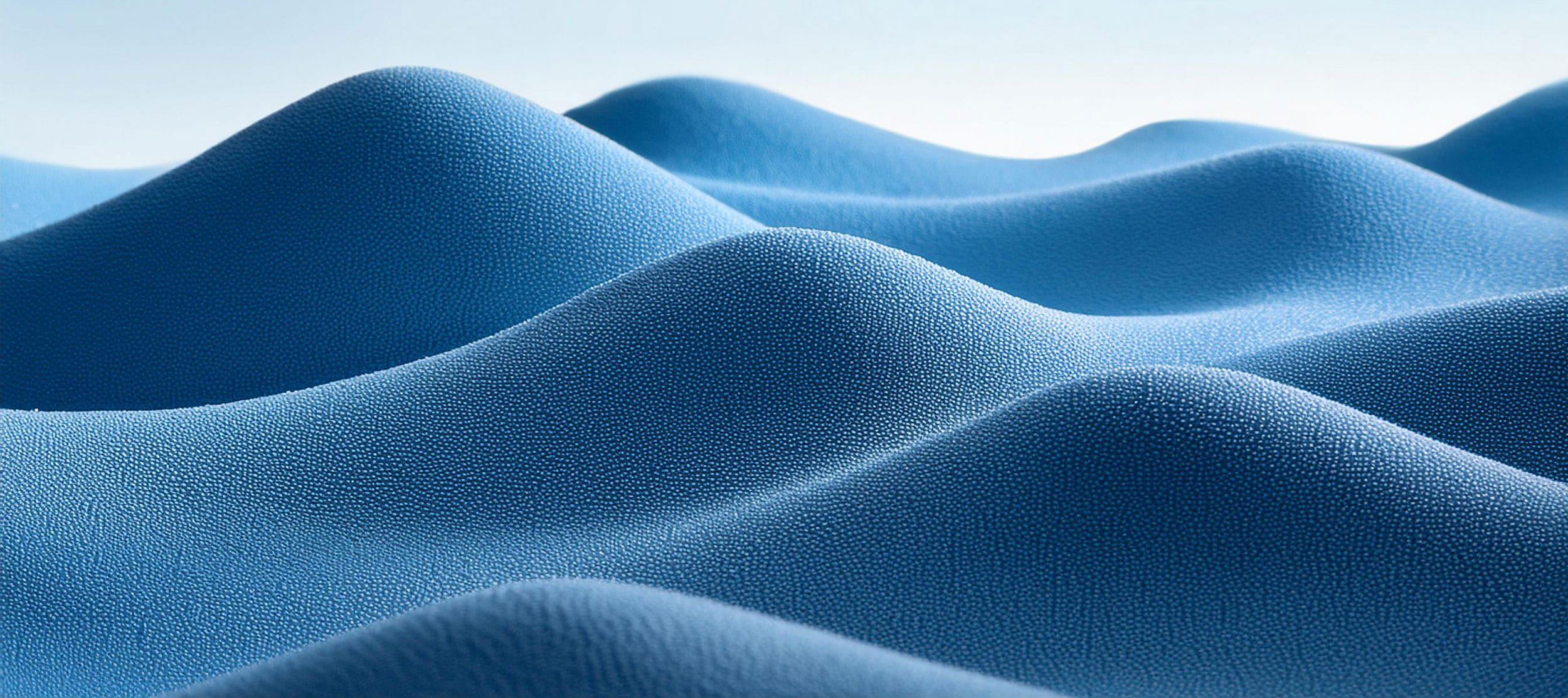
Navigating a dynamic material landscape
March 11th, 2025
As a solution provider, we respond to the evolving material landscape and develop corresponding processes.
share
extrusion technology
New material compositions enhance product quality, create a healthier working environment for operators, and reduce environmental impact. A lot of good reasons to keep innovating.
Sustainable polymers
The push for recyclability and lower CO2 emissions speeds up the transition to eco-friendlier materials.
Low-cost additives
The reasons for switching to new additives are often price related. In high-volume production, reducing the cost per kilometer can achieve substantial overall savings.
High-performance polymers
Rapid advances in technology and innoÂvation have increased the need for materials that can withstand extreme conditions and provide superior performance in critical environments.
Not just swapping one piece of the puzzle
Replacing a proven material component in cable manufacturing with a new one is not as simple as it may sound. A typical drawback is the necessity to reconfigure the entire extrusion process, as alterations in one component often trigger adjustments in others. Changes in material composition affect:
- Extruder and screw design
- Crosshead and tool design
- Process parameters
- Cooling process
- Productivity
All these factors pose challenges for process engineering. They require extensive research and development. And a lot of testing, testing, and more testing. Often with new materials, the process window becomes narrower, leaving operators with less time and flexibility to adjust process parameters. High-precision equipment, a stable process, and continuous quality monitoring become essential for maintaining or even enhancing product quality.
Examples
In 2018, lead was listed as a substance of very high concern (SVHC) by the European Union. Once used in PVC-coated cables for higher speeds and throughput, it has been replaced by other additives. The extrusion process had to be adjusted accordingly to keep up the speed and productivity.
Azodicarbonamide, previously used as a nucleÂating agent in thermoÂplastic foams, has been replaced by safer substances due to health concerns.
This change results in a much narrower process window for foaming.
you may also like
contact
get in
touch
with us